I know Home Automation is supposed to be all about how you can do-it-yourself and the ultimate satisfaction you get when you look at the home theater you have "created," and you fire up a movie for the first time.
However, I'm going to take you down another path to home theater nirvana that still allows you to "get your hands dirty," but in the end gives you a more professional-looking and -sounding home theater for not too much more than what you would have spent doing the entire construction yourself. Believe it or not, it's called "Theater in a Box."
The Goal
Caster Communications specializes in public relations for companies in the consumer electronics industry. Whenever you read a review of a product (in HA, for example), there is usually a good PR company (Caster, for example) behind the manufacturer that made that review happen. I myself used to be a reviewer, so the transition to PR was a natural one. As much as I love my role as Vice President of Caster (PR hack, as my old editor buddies affectionately call me), I missed reviewing products. So, how do I get my hands on the latest gear to play around with and keep my day job? Easy: open a beta testing facility.
Many companies use both professional and amateur beta-testers to provide opinions of their products before the company goes to market with them. It’s like getting the inside scoop on how a reviewer will react to your product before you actually send it to one. Any small mistakes (even the best engineers miss things) that may have been overlooked, that could cause a detrimental review, or costly returns, can be fixed before the unit goes into full-scale production. With me, the manufacturer gets the added benefit of having an actual former reviewer evaluate the product and give it a professionally written evaluation. All I needed was the right facility.
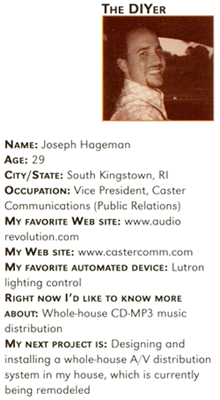
The Challenge
In February of 2001, Caster Communications closed on a beautiful 4,000-square-foot building in Wakefield, RI. On the basement level was a 28 x 20 room that I immediately claimed as my office. (No one else wanted the "dungeon" anyway).
The room has two staircases, one that leads into it from the hallway, and one that leads out to the parking lot above. The thick acoustical drop ceiling is a good height, at about seven feet, eight inches, with heavy insulation up to the sub floor. Unfortunately, there was a small closet on the right-hand side of the front of the room that threw off my center point. That was the first thing that needed to go.
Now,
with an unobstructed front wall, I could start assembling my sound
room. I placed my cinema chairs about 10 feet from the front wall and
set up acoustical treatment in the necessary places. In my previous
sound room in my apartment in New York, I had gotten extremely lucky and
the room turned out to be nearly acoustically perfect. I knew this room
wasn't going to sound as good as that one, but I figured I could
manage. It turned out I couldn't. Even with my two huge subs, the large
room was just swallowing up my bass, my front soundstage just didn't
sound right, and surround-sound effects were getting lost in the back of
the room. I moved around my acoustical treatments. I moved around my
chairs. I moved around my speakers. Little things seemed to improve here
and there, but I never achieved the sound I was looking for.
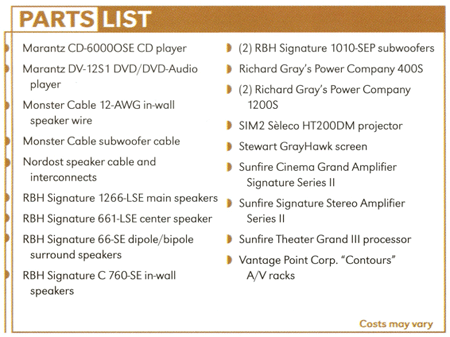
The Professionals
It was time for me to admit I needed help. I maybe really good with gear, but this room was too much for me to handle on my own. I decided to call on Theatre Design Associates (TDA) to help me design and construct a new room in my existing space. I knew I was going to have to split the room in half and flip its orientation, so I knew a wall was going to have to be put up. I told TDA that I wanted to be involved in the process as much as possible, but that I'm no construction guy and I wanted to give them the freedom to do what they do best. We talked about their products and zeroed in on Theater in a Box because it was the easiest and most cost-effective solution that would give me the help I needed, and let me stay involved at the same time.
The first thing I did was map out a list of contractor responsibilities, TDA responsibilities and my responsibilities with Scott Carlson, President of TDA. Scott then laid out the room with me and, just as I had figured, he suggested we put up a wall and flip the orientation of the home theater. What was the left wall would become the back of the home theater. The biggest challenge we faced was a huge metal beam covered by a soffit that ran smack-dab in the middle of the existing room from left to right. This metal beam dictated the new dimensions, so the new room ended up being 20 feet long by 14 feet, 71/2 inches wide. Perfect for what I wanted and, as it turned out, the two closets in the back ended up being perfectly symmetrical (a recurring theme in this project). Our next challenge was how to get the room symmetrical with a soffit running the length of the right wall. The answer (to Scott at least) was simple—mirror that soffit on the other side, and then build new soffits in the front and back of the room, creating what would best be termed a "tray" ceiling. Yet another challenge was the baseboard heating that, once the new wall was built, would only run along the left side and front wall of the theater. Again, Scott suggested we just mirror the baseboard heating covers all the way around the room, to make everything look symmetrical.
After laying out the dimensions of the room, we mapped out all of the equipment placement, and TDA's engineers figured out the tuning of the room in conjunction with the placement of the acoustical treatments. Next came the finish colors and textures. My maple RBH speakers and subwoofers and the maple veneer trim in the room dictated the color scheme, as did the color of the carpet, which I planned on keeping. No use spending extra money where I really didn't have to. Since TDA is a custom company, they were able to source materials and colors that would all match perfectly.
After
all our preliminary plans were done, it was time for the contractors.
They put up the new wall, ripped down the existing soffit that covered
the structural beam (it was too big) and framed in the new soffits. Now
it was my turn. I contacted my good friends at Monster Cable, who
provided me with a spool of 12-gauge specialty in-wall speaker wire and
raw subwoofer cable to run through the soffits before they were
dry-walled in. My plan was to put all my gear in one of the existing
back closets (IR commands would be handled by a hardwired IR receiver
and blaster) and put speaker-level and line-level connections in the
closet wall that would connect to my speaker and subwoofer connections
in the room. This would allow me to easily change product in and out, as
well as hide a lot of the cables to keep the room looking very clean
and uncluttered—a must for anyone who knows the president of Caster, who
also happens to be my wife. I put five-way binding posts for all seven
channels in the closet, as well as two RCA jacks for connection to my
two subwoofers. In the front of the room, I put the binding posts for
the L/C/R speakers and two RCA jacks for the subs. I pre-wired for my
side surround speakers that would be mounted directly onto acoustical
panels, and the rear back in-ceiling surround speakers fit perfectly in
between the studs of the rear soffit, so I screwed the cabinets to the
studs and ran the wire through.
Next came the three-zone Lutron lighting control system. Scott and I decided to put the "master" in an existing four-gang box in my office and make the control in the home theater a "slave" to it. I did some preliminary hookup of the system, but left it up to the electrician to rewire the can-lights in the room so that the lights in the front of the room would be zone one, the lights in the back zone two, and the lights in my office zone three. While the electrician was there I also had him put the Hubbell outlets in the closet, as well as a 220 VAC line for future use, with a Sub Station from Richard Gray's Power Company.
After running all of the wire and making the connections, it was time for the drywall. This process took three days, and I must say my drywall contractor did a fabulous job. After everything was dry, it was my turn to sand down the seams to get ready for painting. This is the point when I wished I had paid the drywall guy to stick around. Sanding drywall has to be the worst job in the entire world. I was blowing drywall dust out of my nose for hours. Dust was everywhere! But I finished, unscathed, and moved on to painting. Oh, by the way, did I mention that at this stage it was five days until my wedding? Needless to say, I was in a rush to get this done.
The Cavalry Arrives
Day two of painting, and the TDA guys show up in a huge truck packed with all my acoustical treatments, my sofa, and enough tools to tackle anything they might encounter. These guys came prepared. Tony the Tiger (he had a Tiger tattoo) and Tony (Antonio as I called him) took a survey of what was complete: The walls and soffits were up, all the wire was run, and the room was about 25 percent painted. They made an executive decision—they both grabbed paintbrushes and started painting. I loved these guys already.
After the painting of the walls and the baseboard heating elements, Tony laid the carpet back down and Antonio went to work on putting up the baseboard heating covers and cutting them to fit! Next came painting the acoustical tiles in the tray portion of the ceiling. Early in the development phase, I expressed some concern about dry-walling over the entire ceiling, due to plumbing, HVAC and electrical wires that might need to be accessed some day. That's when TDA came up with the plan of incorporating the acoustical tiles into the plan by building the soffits all the way around the room, leaving the tiles in the center, and creating the tray ceiling. Not only does this give me the access I need, it also gives the illusion that the ceiling is higher than it really is.
The next day brought the acoustical treatments. For the most part, the process of putting up the acoustical treatments went very smoothly, and Tony did a fantastic job of mentally mapping out the room and making sure everything was symmetrical and put where it was supposed to be acoustically.
Day three was spent mostly on putting the aesthetic treatments into the room, such as the columns and the inserts in the "ring" of the tray ceiling. Putting in the columns in the front of the room proved a little challenging, because the ceiling of the front soffit wasn't exactly straight. It sloped a bit to the right so the column fit snug on the left, but left a decent gap on the right. TDA knew this well in advance because of the measurements I had given them, so Antonio was able to compensate by trimming a strip of metal that was painted black and gluing it to the top of the column so that the gap was completely covered.
After the aesthetic treatments were in, it came time to hang the screen. Tony had done this task a hundred times, so this went by fairly quickly. I had somehow lost the brackets for hanging the screen mount, so Tony just fashioned brackets from some parts he had on hand. Next came the shelf for the projector. Initially I had wanted to cut a hole in the drywall between the two back closets to put the projector into. But because of a stud and some electrical wires, it wasn't possible. I discussed this with Scott and he said that was no problem and that his guys would just make up a shelf at their facility. Sure enough, Tony busted out a pre-painted, decorative shelf made from MDF, and started bolting it I to the wall. We cut a hole in the wall directly behind the SIM2 projector to snake the video and AC cable through to the inside of the closet.
All that was left for the Tony(s) was to haul in the sofa and go have a well-deserved beer. As for me, well, I still had to hook up all of the equipment. I put all of my gear in the back closet, including my new Sunfire gear and Marantz DVD/DVD-A player. At this point it was about four hours until our rehearsal dinner, and one day until the wedding. So I basically threw everything in there, turned it on just to make sure it was working properly, then left it for about three weeks while I got married and went on my honeymoon.
The Verdict
So, was all that really worth it? Did spending almost $27K on a new home theater really make that big a difference? You betcha! Everything sounds better. I actually have a front soundstage now, and surround-sound effects are incredible! The bass didn't come as easily as I had hoped. I had always had the feeling that placing the subs in the front of the room wouldn't be the best spot for them. I've usually had better success with subs when placing them along the sides of the wall. Sure enough, the same thing applied here. The baseboard heating hides the subwoofer cable that comes out from the front of the room so that's not that big a deal. One last concern—Scott had mentioned HVAC to me and wondered how I was going to get fresh air in the room. I decided to forgo the expense of tapping into the main line that runs through the ceiling to supply air upstairs, and then see how it went. My contractor said that it was no problem to address this later and it wouldn't disturb the finished room. As it is, the room is below grade, so it is always cool down there, and I keep the door open when I am not using the room. So far it hasn't been a problem.
As much as I like to think of myself as an A/V professional, I can admit when it is better to leave certain things up to the real pros. So, if you're itching for a home theater in your house but you don't know where to start, or just don't think you can do it the way it ought to be done, call a home theater design company—a killer home theater is a lot more affordable than you may think.
One thing I failed to mention—all of the planning for this project was done over the phone, fax and email. I didn't have to spend any money on travel arrangements for TDA to come out and spec out the room. They didn't show up until it was time for the installation. It didn't matter that we were a thousand miles away from one another—TDA knew the right questions to ask, and it was up to me to tell them what I wanted and give them proper measurements
Many, many thanks go to Scott, Rick VanDerSnick, Tony Krueger and Tony Medina, and whoever else at Theatre Design Associates worked on my room. A thanks also goes to Bob Leonard of Merchant Construction, for constructing my room on such short notice. Of course, I wouldn't have any sound in my sound room if it weren't for the generous support of Monster Cable, Nordost, and Caster's own clients: RBH Sound, Richard Gray's Power Company, SIM2 Sèleco USA, Sunfire and Vantage Point Corporation.
Manufacturers interested in the beta testing room can log onto the Caster Web site for a 360-degree virtual tour of the "Caster Theater" and an in-depth explanation of the beta testing services.